What’s driving the future of the material handling sector?
Autonomous robots. Next-generation battery platforms. Greater power — with a sharper focus on safety and uptime.
As labor shortages persist and uptime becomes critical to meeting tight deadlines and tighter margins, manufacturers are rethinking how they move goods, power equipment and scale operations.
At ProMat and LogiMAT 2025, one thing was clear: the future hinges not just on automation, but on the energy systems that keep these innovations running. Several trends emerged that will define what’s next — and demonstrate why making lithium work has never mattered more.
The future is now: A rise in automation and robotics in material handling
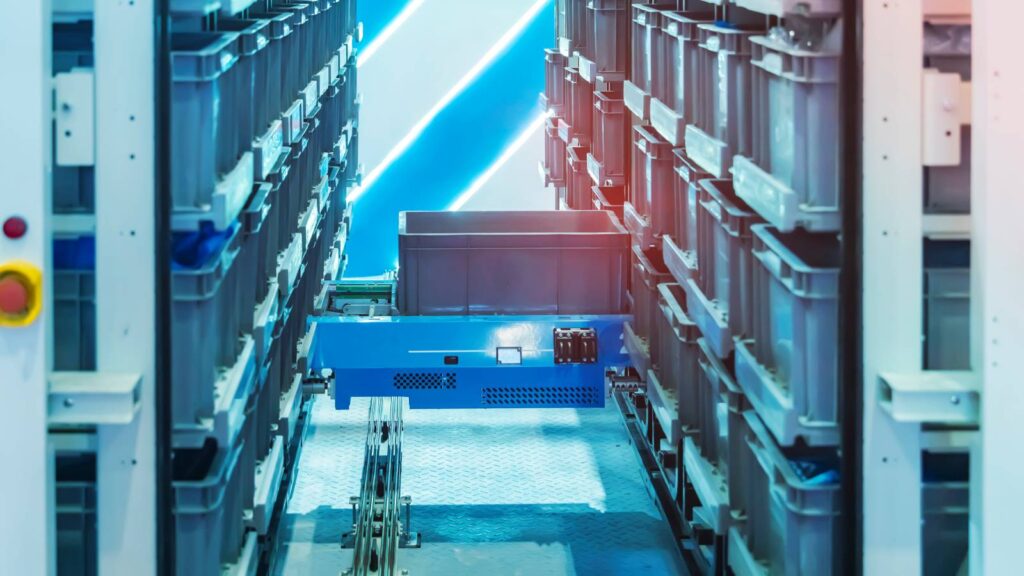
Automation continues to reshape manufacturing and logistics. As the industry faces persistent labor shortages, OEMs are increasing their investments in autonomous systems —ranging from AMRs to humanoid robots.
Key trends in this area include:
- A surge in AMRs and AGVs: Robots capable of 100+ picks or placements per hour day for two working shifts are now becoming more common in warehouses and manufacturing settings.
- Robot-as-a-Service (RaaS): Leasing is on the rise, with companies prioritizing uptime and performance over equipment ownership.
- Early humanoid adoption: Robotics companies like Agility Robotics are piloting humanoids in Amazon warehouses, moving lightweight materials (up to 35 lbs.) and performing functional tasks once thought impossible.
These sophisticated systems come with specific power needs.
Opportunity charging to improve Uptime
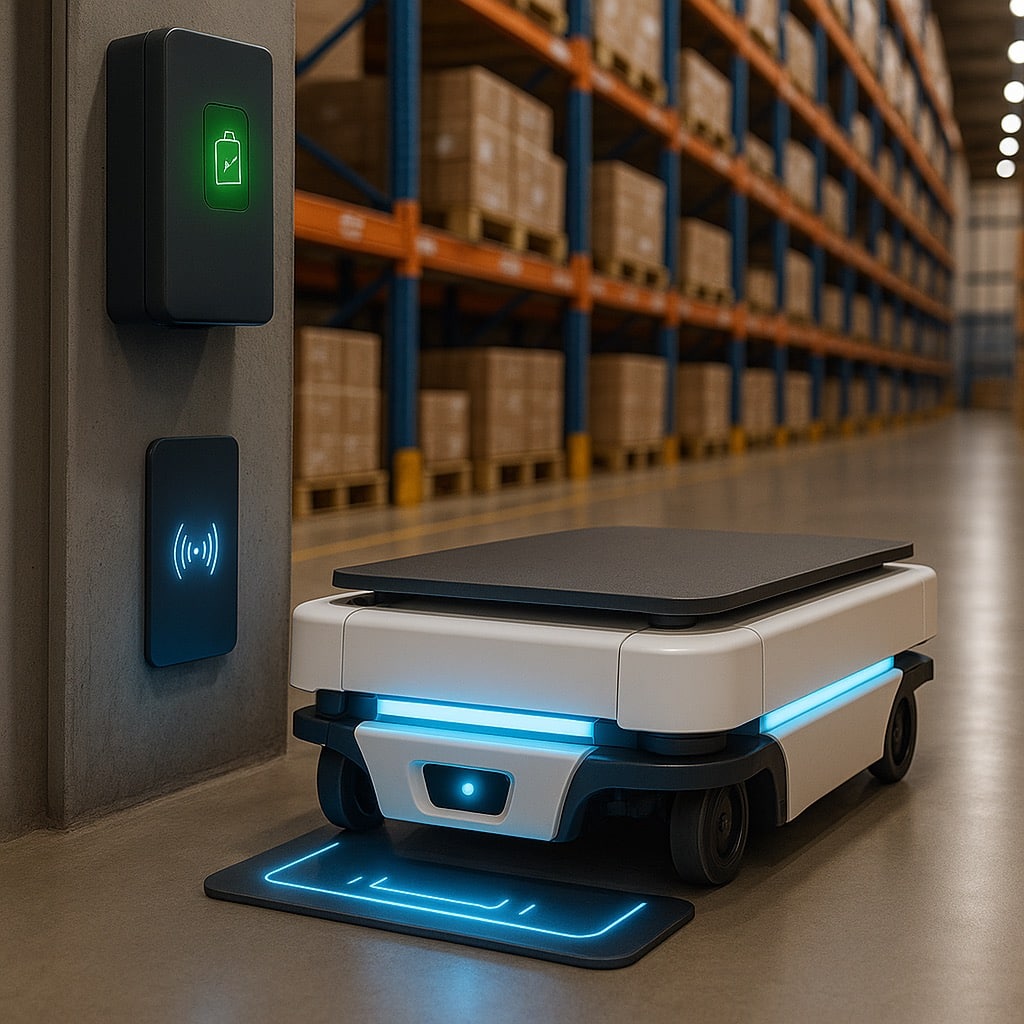
Keeping these innovative fleets moving requires rethinking how and when you charge what are essentially a version of electric vehicle batteries. This drives a transition away from traditional lead-acid power systems in favor of solutions that support opportunity charging — quick top-off charges lasting just 10 to 15 minutes.
Lead-acid batteries are ill-suited for opportunity charging because charging must wait for a full discharge, leading to longer downtimes and costly operational gaps.
Lithium-ion batteries used to power these electric vehicles, by contrast, can handle brief, frequent charges without any memory effect. This allows equipment to plug in and top off between tasks, maximizing uptime and operational efficiency.
Plug-and-play simplicity to reduce maintenance
Today’s equipment is moving toward plug-and-play, maintenance-free power sources.
Whether it’s robots, AMRs, or humanoids, the goal is the same:
- Eliminate coolant systems, watering routines, and heavy maintenance.
- Reduce downtime and total cost of ownership.
- Increase operational reliability across the board.
High Voltage power systems for greater efficiency
As equipment becomes more autonomous and uptime expectations rise, the need for faster energy replenishment and greater system efficiency is pushing manufacturers to rethink their power architectures — starting with voltage. More is better, and here’s why.
In AGVs, an industry-wide transition from 24V/36V to 48V systems is under way. Along with that, forklifts are also moving to 80V platforms for improved energy distribution, reduced current demand and greater operational efficiency, with OEMs like Toyota and Hyster-Yale leading the way. Already on the horizon are glimmers of expanding capacity to as much as 350V-400V.
Along with greater system efficiency, the benefits of these higher voltage systems are many, including reduced cabling size and reduced copper costs. More significantly, these higher voltage power systems support heavier payloads, meaning a single robot can now move two or three loaded pallets at one time.
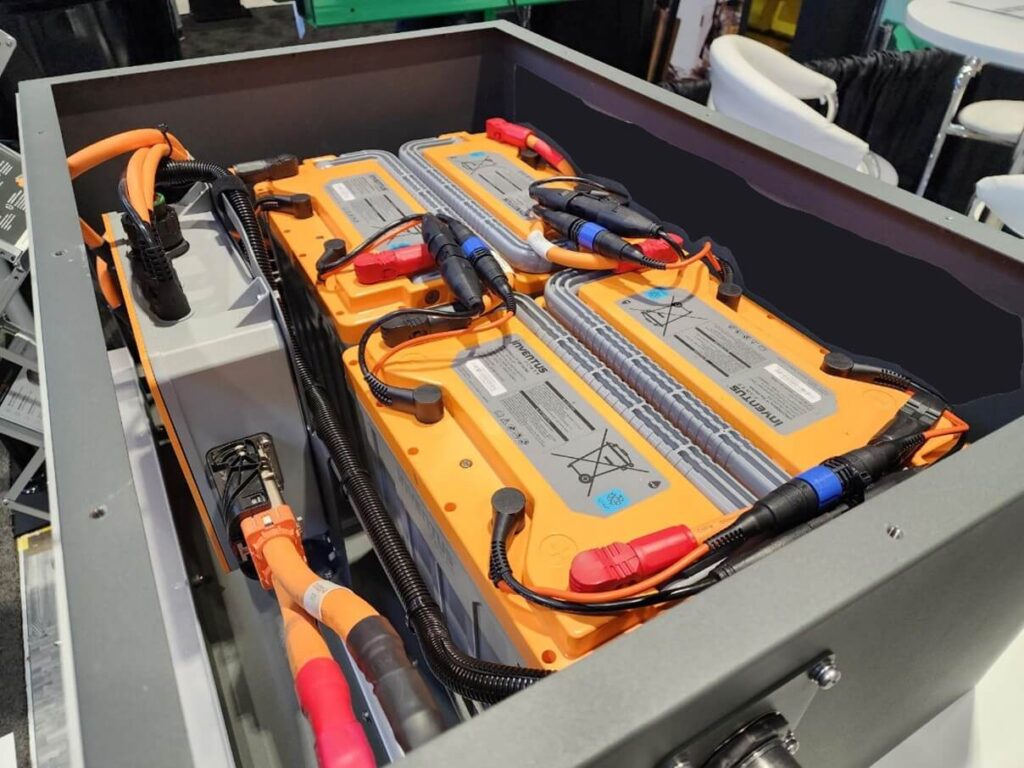
Lithium-ion batteries: Making the switch
Until recently, transitioning to lithium-ion battery systems in material handling equipment raised questions: Is now the right time? Do the benefits outweigh the costs?
Today, lithium-ion is becoming the standard for modern material handling equipment. Its advantages over lead-acid are clear:
- 30-40% greater energy efficiency which saves on electricity costs
- Opportunity charging for faster recharge time
- Maintenance-free operation (no watering or ventilation needed)
- Modularity — the ability to scale battery packs and energy based on asset utilization
Another key advantage of lithium-ion adoption is the ability to integrate seamlessly with IoT platforms for smarter fleet management. Asset tracking, battery health monitoring, and usage optimization are becoming essential tools as automation fleets expand — and lithium systems make real-time visibility possible.
Design and safety factors for lithium-ion systems
Lithium-ion batteries can operate safely and effectively with a robust Battery Management System (BMS). Properly designed systems help batteries resist damaging energy spikes, which is important when operating rough, suspension-free material handling environments.
- Resist damaging energy spikes — critical for rugged, suspension-free warehouse environments
- Maintain uptime even under heavy or continuous use
- Extend battery lifespan across a range of temperatures, including cold storage
Lithium-ion systems with integrated heaters are helping material handling equipment operate reliably in refrigerated warehouses and outdoor cold environments. OEMs increasingly demand battery designs that maintain performance across wide temperature swings, from subzero cold storage to high-heat outdoor yards.
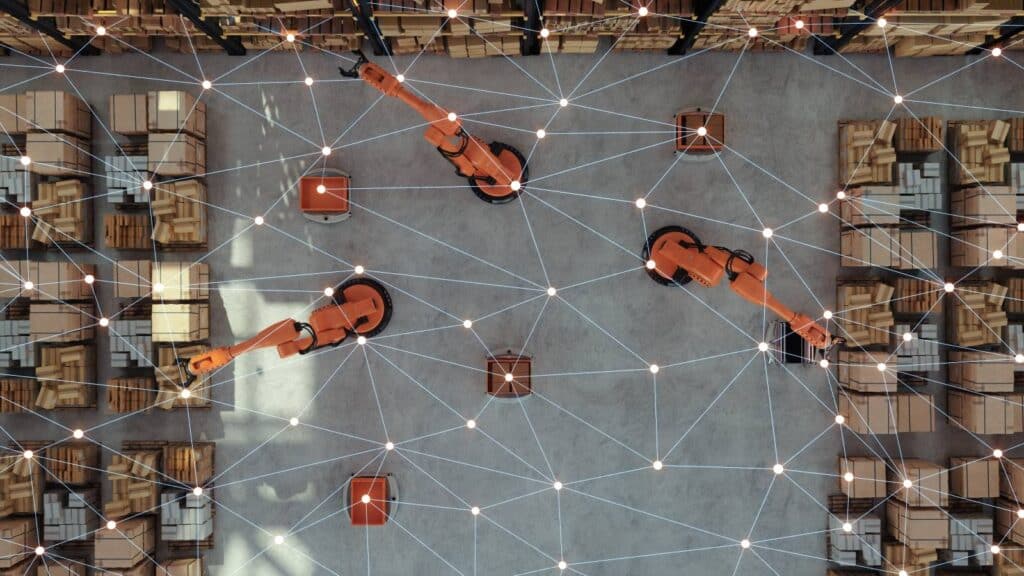
Meeting emerging regulations
Emerging regulations are also shaping design considerations. States like Washington and New York are introducing new warehouse safety standards, limiting battery State of Charge (SOC) to below 30% during storage.
OEMs are increasingly prioritizing UL-certified lithium battery solutions to meet insurance requirements and safety regulations.
Making it work: Why early battery system partnerships matter
The battery and its system shouldn’t be an afterthought. They’re the heart and brain of these autonomous systems and the earlier it’s integrated into your design, the better. The worst thing that can happen is the battery doesn’t work — and the equipment can’t even power on. That’s why proper design and validation are critical.
Selecting the right battery partner early in the design process pays off long-term. Here’s why:
Early collaboration means better integration: Designing around the right power system ensures compliance, efficiency, and proper scaling from the outset.
Platform architecture matters: Scalable, modular battery platforms allow OEMs to adapt the same system across multiple equipment types — mobile robots, forklifts, cleaning machines — without starting over each time.
Steering clear of commodity pitfalls: Not all lithium batteries perform equally. Strategic partners validate systems, meet evolving regulations and can deliver software updates to extend battery life and enhance performance over time.
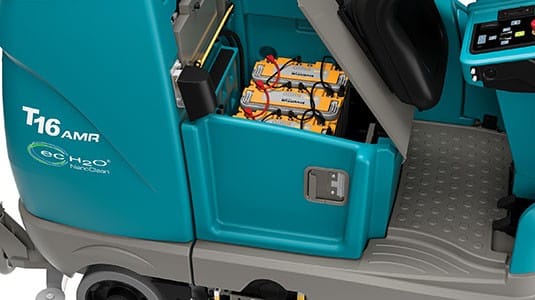
Image Source: Tennant Company
Powering the future of the material handling industry
As performance demands rise and automation takes off, material handling systems must be built for efficiency, flexibility and safety from the start. Power architecture is part of your strategic decision.
Lithium-ion solutions, paired with the right integration and oversight, are proving essential to the next generation of equipment. For OEMs and system designers alike, early collaboration is key to keeping innovation moving.
Interested in solutions that help you automate and scale? Connect with an expert at Inventus Power.